自動滾絲機的加工精度和質量控制方法主要涉及以下幾個方面:
一、加工精度控制
精密的液壓控制系統:
自動滾絲機通常采用先進的液壓傳動系統,能夠控制滾絲輪的運動。
液壓控制系統可以根據預設的加工參數,準確地調節滾絲輪的轉速、進給量等,從而確保螺紋的螺距、牙型等各項參數都能達到極高的精度要求。
定期校準:
隨著滾絲機的使用,其加工精度可能會出現偏差。
因此,需要定期(如半年或一年)對滾絲機進行精度校準。
可以使用的工具(如螺紋塞規、環規等)對加工出來的螺紋進行,并根據結果調整滾絲機的參數。
檢查機器幾何精度:
定期對機器的直線度、平行度等幾何精度進行檢查。
通過調整機器的地腳螺栓、導軌等部件,使機器恢復到規定的精度范圍內。
二、質量控制方法
選擇高質量的材料:
滾絲輪是自動滾絲機的關鍵部件,其質量和精度直接影響到螺紋的加工質量。
因此,在選擇滾絲輪時,應確保其材質優良、精度高,并且與待加工螺紋規格相匹配。
優化加工參數:
根據具體的加工需求和工件材料,合理設置滾絲機的加工參數(如滾壓速度、進給量、滾壓深度等)。
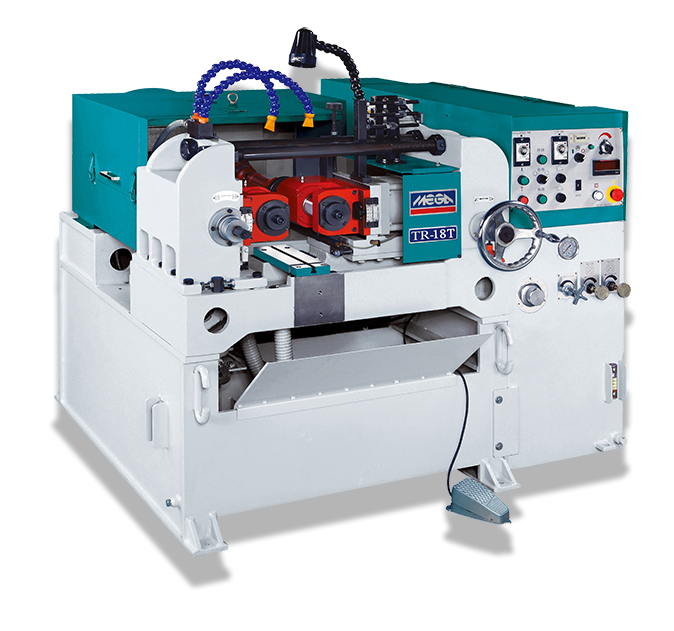
這些參數的設置將直接影響滾壓和工件的質量,因此需謹慎考慮并結合實際情況進行調整。
持續監控加工過程:
在滾壓過程中,應持續監控設備的運轉情況和加工。
如發現異常(如振動、噪音過大等),應立即停機檢查并調整參數或采取其他措施進行修正。
使用冷卻液和潤滑油:
冷卻液可以滾壓區域的溫度,減少熱變形和磨損;
潤滑油可以減小滾絲輪與工件之間的摩擦系數,提高滾壓和工件表面質量。
嚴格的規程:
人員應經過培訓并熟悉自動滾絲機的結構、原理和方法。
在過程中,應嚴格遵守規程和加工流程,確保加工過程的穩定性和穩定性。
的檢修和維護:
定期對自動滾絲機進行的檢修和維護工作,包括機械部件、電氣系統、液壓系統等。
拆開機器的部分部件,檢查內部的磨損情況和隱藏的故障隱患,并對發現的問題進行徹底的維修和更換磨損嚴重的部件。